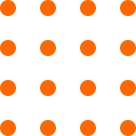
Product Shelf Life refers to the period during which a product retains its intended function. The Expiration Period denotes the timeframe after which a medical device may no longer perform as expected.
To determine whether a specific device requires a defined shelf life and to establish its expiration period, manufacturers must assess multiple parameters. A comprehensive analysis should be conducted to assess whether degradation within the designated timeframe could lead to functional failures and to determine the associated risk level.
For certain devices, such as tongue depressors, specifying a shelf life may be unnecessary due to their minimal risk of time-dependent degradation and negligible consequences of failing to fulfill its intended function.
Conversely, for degradable devices used in life-threatening conditions (e.g., pacemakers), the failure rate during the labeled shelf life should be close to zero. When evaluating medical device shelf life, the following aspects should be considered:
Chemical Properties
- Degradation: Do active ingredients/components degrade over time in a manner that adversely affect safety or performance?
- Interactions: Do components interact in ways that alter the device? Could interactions among components compromise its ability to function as intended?
- Device-Packaging Interactions: Are there any adverse interactions between the device and its packaging?
- Radioactive Decay: Does the device contain short-half-life radioactive materials? Do decay byproducts compromise safety or efficacy?
- Manufacturing Impact: Do manufacturing processes alter the chemical properties of raw materials, components, or finished devices in ways that impair safety or performance?
Physical Properties
- Physical Characteristics: Do physical traits (e.g., appearance, viscosity, elasticity, tensile/burst strength, electrical resistance) change over time? Even cosmetic changes may raise concern among users.
- Production Effects: Do manufacturing processes negatively impact the physical properties of components or finished devices?
- Storage Conditions: Could storage factors (e.g., temperature, humidity, light exposure) negatively affect device safety or performance?
Microbiological Considerations
- Sterility: Does the sterile device maintain sterility? This depends on packaging integrity and seal integrity.
- Environmental Controls: Are microbial load controls required during manufacturing/storage to prevent adverse degradation?
- Antimicrobial Efficacy: Does the device lose its intended antimicrobial functionality?
- Barrier Integrity: Is the barrier protection compromised?
- Preservative Efficacy: How long can preservative systems maintain effectiveness within tolerance limits?
Therapeutic Performance
- Does the device’s ability to deliver therapeutic or diagnostic functions degrade under storage/usage conditions?
Toxicological Risks
-
Do degradation byproducts with toxic effects form during storage/use?
Biocompatibility
- Does the device’s biocompatibility deteriorate adversely over time?
Additional Factors Affecting Shelf Life:
- Storage Conditions: Temperature fluctuations, humidity, ventilation, air pressure, visible light, and other radiation exposure.
- Device Nature/Intended Use: For Example: Latex medical gloves degrade naturally over time due to material‘s inherent properties.
- Component Degradation: Devices containing batteries or other components with time-sensitive functionality may experience performance degradation over time.
- Manufacturing Methods: Sterile-packaged IVD devices may have a shorter shelf life compared to those that undergo periodic sterilization.
- Packaging: The surface area-to-volume ratio of the product in its packaging may impact stability, leading to variations in shelf life across different container sizes.
- Transportation Conditions: Factors such as vibration, mechanical shock, temperature, humidity variations.
Device shelf life should not be confused with service life (operational lifespan after deployment).
Regulatory Considerations
For 510(k) submissions, accelerated stability studies are typically provided to support the designated shelf life. However, real-time stability studies are required for heat-sensitive products (e.g., chemical sterilization indicators).
This translation maintains technical precision while ensuring readability for regulatory or professional audiences. Let me know if you need further refinements!